Laser cleaning for removing adhesive residues
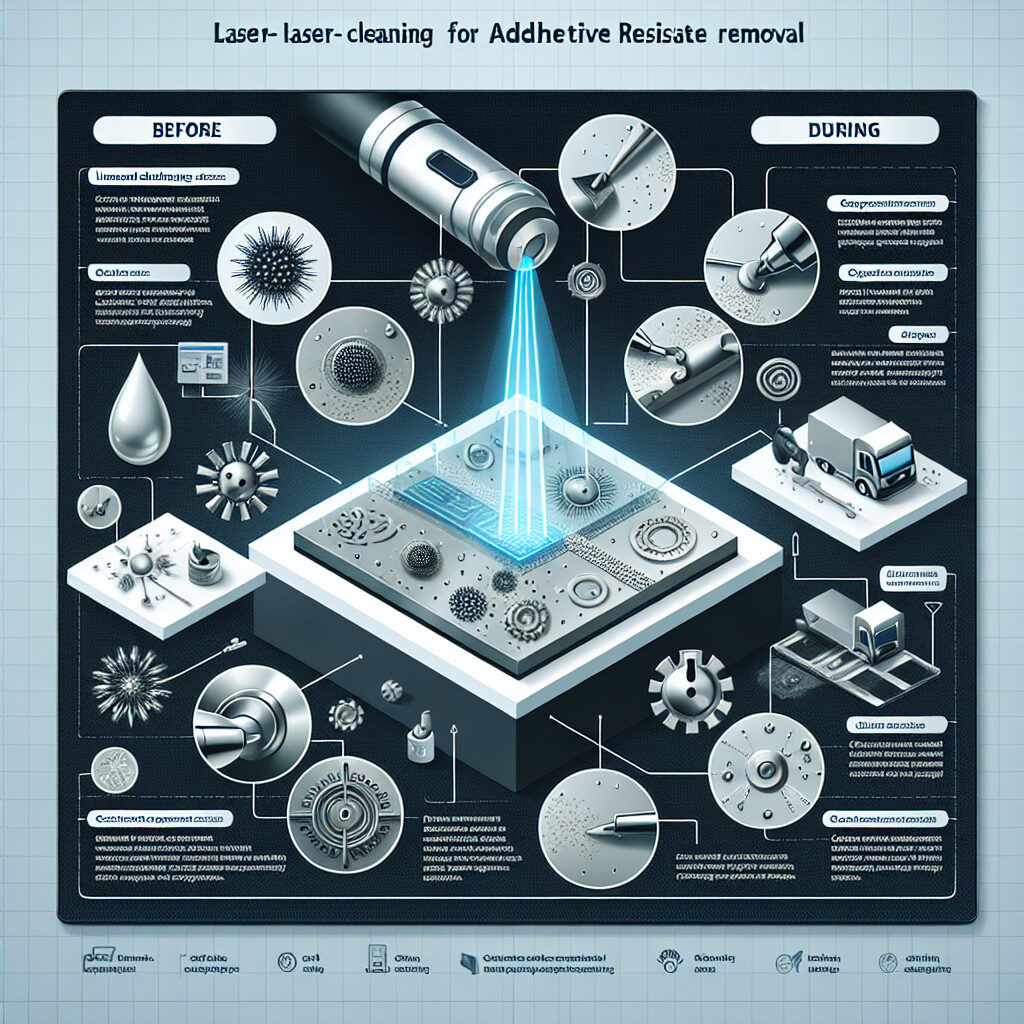
- Benefits of Laser Cleaning for Removing Adhesive Residues
- How Laser Cleaning Works on Adhesive Residues
- Comparison of Laser Cleaning vs Traditional Cleaning Methods for Adhesive Residues
- Safety Considerations for Laser Cleaning of Adhesive Residues
- Applications of Laser Cleaning in Industrial Settings for Adhesive Residues
Benefits of Laser Cleaning for Removing Adhesive Residues
Adhesive residues can be a stubborn and frustrating problem to deal with, especially when traditional cleaning methods fail to completely remove them. However, laser cleaning offers a highly effective and efficient solution for removing adhesive residues from various surfaces. Here are some of the key benefits of using laser cleaning for this purpose:
1. Non-contact cleaning: Laser cleaning is a non-contact process, which means that there is no physical contact between the cleaning equipment and the surface being cleaned. This eliminates the risk of damage to delicate surfaces and ensures a gentle yet thorough cleaning process.
2. High precision: Laser cleaning allows for precise control over the cleaning process, making it possible to target specific areas and remove adhesive residues with pinpoint accuracy. This level of precision is particularly useful for cleaning intricate or complex surfaces.
3. Environmentally friendly: Laser cleaning is a clean and environmentally friendly process that does not require the use of harsh chemicals or solvents. This makes it a safer and more sustainable option for removing adhesive residues, especially in sensitive or regulated environments.
4. Fast and efficient: Laser cleaning is a fast and efficient process that can remove adhesive residues quickly and effectively. This can help to reduce downtime and increase productivity, making it a cost-effective solution for cleaning applications.
5. Versatile: Laser cleaning can be used to remove adhesive residues from a wide range of surfaces, including metal, plastic, glass, and more. This versatility makes it a versatile cleaning solution for a variety of industries and applications.
6. Reduced maintenance: Laser cleaning can help to reduce the need for regular maintenance and cleaning of equipment and surfaces, as it can effectively remove adhesive residues and other contaminants in a single pass. This can help to extend the lifespan of equipment and reduce maintenance costs over time.
7. Safe and easy to use: Laser cleaning is a safe and easy-to-use process that requires minimal training and expertise. This makes it a user-friendly option for cleaning adhesive residues, even for operators with limited experience.
In conclusion, laser cleaning offers a range of benefits for removing adhesive residues, including non-contact cleaning, high precision, environmental friendliness, speed and efficiency, versatility, reduced maintenance, and ease of use. These advantages make laser cleaning a highly effective and practical solution for cleaning adhesive residues from a variety of surfaces.
How Laser Cleaning Works on Adhesive Residues
Adhesive residues can be a stubborn and frustrating problem to deal with, especially when traditional cleaning methods fail to remove them completely. However, laser cleaning offers a highly effective and efficient solution for removing adhesive residues from a variety of surfaces. In this article, we will explore and why it is such a powerful cleaning method.
What is Laser Cleaning?
Laser cleaning is a non-contact cleaning method that uses a high-energy laser beam to remove contaminants from surfaces. The laser beam is focused on the surface of the material, where it rapidly heats and vaporizes the contaminants, leaving behind a clean surface. Laser cleaning is highly precise and can be used on a wide range of materials, including metals, plastics, ceramics, and composites.
How Does Laser Cleaning Work on Adhesive Residues?
When it comes to removing adhesive residues, laser cleaning is particularly effective because it can target and vaporize the adhesive without damaging the underlying material. The laser beam is able to penetrate the adhesive layer and break down its molecular bonds, allowing the residue to be easily removed from the surface. This process is highly controlled and can be adjusted to suit the specific requirements of the cleaning task.
Benefits of Laser Cleaning for Adhesive Residues
There are several key benefits to using laser cleaning for removing adhesive residues:
1. Efficiency: Laser cleaning is a highly efficient cleaning method that can remove adhesive residues quickly and effectively.
2. Precision: Laser cleaning is a precise cleaning method that can target specific areas of the surface without causing damage to surrounding areas.
3. Non-contact: Laser cleaning is a non-contact cleaning method, which means that there is no physical contact between the cleaning equipment and the surface being cleaned. This reduces the risk of damage to delicate materials.
4. Environmentally friendly: Laser cleaning is an environmentally friendly cleaning method that does not require the use of harsh chemicals or solvents.
5. Cost-effective: While laser cleaning equipment can be expensive, the long-term cost savings of using laser cleaning for adhesive residues can be significant.
Applications of Laser Cleaning for Adhesive Residues
Laser cleaning is a versatile cleaning method that can be used in a wide range of industries and applications. Some common applications of laser cleaning for adhesive residues include:
– Removing adhesive residues from automotive parts
– Cleaning adhesive residues from electronic components
– Removing adhesive residues from medical devices
– Cleaning adhesive residues from aerospace components
Conclusion
In conclusion, laser cleaning is a highly effective and efficient cleaning method for removing adhesive residues from a variety of surfaces. Its precision, non-contact nature, and environmentally friendly properties make it an ideal choice for cleaning tasks where traditional methods may fall short. If you are struggling to remove adhesive residues from your surfaces, consider using laser cleaning as a powerful solution.
Comparison of Laser Cleaning vs Traditional Cleaning Methods for Adhesive Residues
Traditional Cleaning Methods
1. Chemical Solvents 🧪
– Chemical solvents are commonly used to dissolve adhesive residues. However, they can be harsh on surfaces and may leave behind harmful residues.
– Some solvents are also flammable and pose a risk to the environment.
2. Mechanical Scrubbing 🔨
– Scrubbing with abrasive tools can be effective in removing adhesive residues, but it can also cause scratches and damage to the surface.
– It is time-consuming and labor-intensive.
3. Heat Treatment 🔥
– Applying heat to adhesive residues can soften them, making them easier to remove. However, excessive heat can damage the surface.
– Heat treatment may not be suitable for all types of materials.
Laser Cleaning
1. Non-contact Cleaning 👀
– Laser cleaning is a non-contact method, which means there is no physical contact with the surface. This reduces the risk of damage.
– It is suitable for cleaning delicate surfaces that cannot withstand abrasive methods.
2. Precision Cleaning 🎯
– Laser cleaning allows for precise control over the cleaning process, making it possible to target specific areas without affecting the surrounding areas.
– It is ideal for removing adhesive residues from intricate or hard-to-reach areas.
3. No Chemicals or Abrasives 🌿
– Laser cleaning does not require the use of chemicals or abrasive tools, making it an environmentally friendly option.
– It eliminates the need for harsh solvents that can be harmful to both the environment and human health.
4. Efficient and Time-saving ⏱️
– Laser cleaning is a fast and efficient method, reducing the time and labor required for cleaning adhesive residues.
– It can be used for both small-scale and large-scale cleaning projects.
Conclusion
In conclusion, laser cleaning offers several advantages over traditional cleaning methods when it comes to removing adhesive residues. It is a non-contact, precise, and environmentally friendly method that can save time and labor. While traditional methods like chemical solvents and mechanical scrubbing may still be effective in some cases, laser cleaning is a promising alternative for delicate surfaces and intricate cleaning tasks. Consider using laser cleaning for your next adhesive residue removal project and experience the benefits firsthand.
Safety Considerations for Laser Cleaning of Adhesive Residues
Adhesive residues can be a stubborn and challenging problem to deal with, especially when traditional cleaning methods fall short. Laser cleaning has emerged as a powerful and effective solution for removing adhesive residues from various surfaces. However, it is important to consider safety precautions when using laser cleaning technology to avoid potential hazards. Here are some safety considerations to keep in mind:
1. Protective Gear: When using laser cleaning equipment, it is essential to wear appropriate protective gear to shield yourself from potential hazards. This includes safety goggles to protect your eyes from the intense laser light, as well as gloves and a lab coat to protect your skin from any stray laser beams.
2. Ventilation: Laser cleaning can produce fumes and vapors as it removes adhesive residues from surfaces. It is important to ensure proper ventilation in the workspace to prevent the buildup of harmful gases. Consider using a fume extraction system to remove any airborne contaminants and maintain a safe working environment.
3. Fire Safety: Laser cleaning generates heat as it interacts with the adhesive residues on surfaces. It is crucial to be mindful of the potential fire hazards associated with laser technology. Keep flammable materials away from the laser cleaning area and have fire extinguishing equipment readily available in case of emergencies.
4. Training and Certification: Proper training and certification are essential for anyone using laser cleaning equipment. Make sure that operators are well-trained in the safe and effective use of the technology to minimize the risk of accidents or injuries. Consider enrolling in a laser safety course to enhance your knowledge and skills.
5. Equipment Maintenance: Regular maintenance of laser cleaning equipment is crucial to ensure its safe and efficient operation. Check for any signs of wear and tear, and promptly address any issues to prevent malfunctions or accidents. Follow the manufacturer’s guidelines for maintenance and servicing to keep your equipment in top condition.
6. Environmental Considerations: Laser cleaning can produce noise and vibrations that may impact the surrounding environment. Consider the noise levels in your workspace and take measures to minimize any disturbances. Additionally, be mindful of the potential impact of laser cleaning on the environment and follow proper disposal procedures for any waste generated during the cleaning process.
7. Radiation Safety: Laser cleaning equipment emits laser radiation, which can be harmful if not properly controlled. Ensure that your equipment complies with safety regulations and guidelines for laser radiation exposure. Use appropriate shielding and barriers to prevent accidental exposure to laser beams and minimize the risk of radiation-related injuries.
In conclusion, laser cleaning of adhesive residues can be a highly effective and efficient solution, but it is important to prioritize safety considerations to prevent accidents and ensure a safe working environment. By following these safety guidelines and precautions, you can enjoy the benefits of laser cleaning technology while minimizing the risks associated with its use. Stay safe and happy cleaning! 🌟🔧👷♂️
Applications of Laser Cleaning in Industrial Settings for Adhesive Residues
How Does Laser Cleaning Work?
Laser cleaning works by using a high-powered laser beam to vaporize or ablate the adhesive residue from the surface. The laser beam is focused on the residue, causing it to heat up rapidly and evaporate, leaving behind a clean surface. The process is non-contact, meaning that there is no physical contact between the laser and the surface being cleaned, reducing the risk of damage to delicate materials or surfaces.
Benefits of Laser Cleaning for Adhesive Residues
- Efficiency: Laser cleaning is a fast and efficient method of removing adhesive residues, reducing downtime and increasing productivity in industrial settings.
- Precision: Laser cleaning can be controlled with high precision, allowing for targeted removal of adhesive residues without damaging the underlying surface.
- Environmentally Friendly: Laser cleaning does not require the use of chemical solvents or abrasive materials, making it an environmentally friendly cleaning solution.
- Safety: Laser cleaning eliminates the need for manual labor and reduces the risk of exposure to harmful chemicals or abrasive materials.
Applications of Laser Cleaning in Industrial Settings
Laser cleaning can be used in a wide range of industrial settings to remove adhesive residues from surfaces and equipment. Some common applications include:
- Manufacturing: Laser cleaning can be used to remove adhesive residues from manufacturing equipment, such as molds, dies, and tools, ensuring optimal performance and product quality.
- Automotive: Laser cleaning can be used to remove adhesive residues from car parts, such as body panels and windshields, improving the appearance and functionality of the vehicle.
- Aerospace: Laser cleaning can be used to remove adhesive residues from aircraft components, such as engine parts and landing gear, ensuring safety and reliability in flight.
- Electronics: Laser cleaning can be used to remove adhesive residues from electronic components, such as circuit boards and connectors, improving performance and longevity.
Conclusion
Laser cleaning is a versatile and effective technology for removing adhesive residues in industrial settings. Its efficiency, precision, and environmental friendliness make it a preferred method for cleaning surfaces and equipment. As technology continues to advance, laser cleaning will likely become an essential tool in the manufacturing and maintenance of industrial equipment.
- Laser cleaning for removing adhesive residues - 25 July 2024
- The safety considerations of laser cleaning - 16 April 2024
- Applications of laser cleaning in the automotive industry - 21 January 2024