The safety considerations of laser cleaning
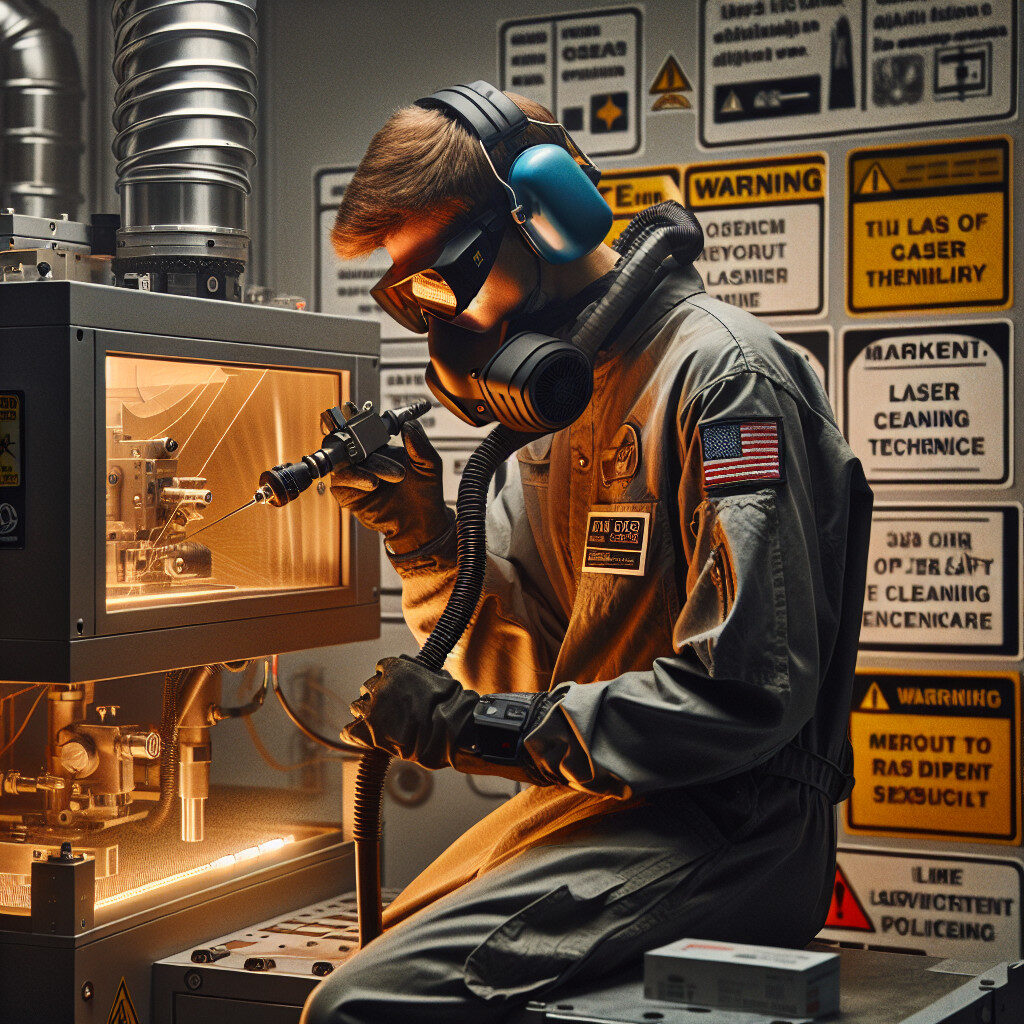
- The principles of laser cleaning and how it works
- The different types of lasers used for cleaning applications
- The safety precautions and regulations for using lasers in cleaning processes
- The potential hazards of laser cleaning and how to mitigate them
- The potential applications of laser cleaning in different industries
- The potential health effects of exposure to laser cleaning emissions
- The role of quality control measures in ensuring the effectiveness and safety of laser cleaning processes
- The potential impact of laser cleaning on worker productivity and efficiency
The principles of laser cleaning and how it works
How laser cleaning works
The process of laser cleaning involves several key principles:
- Absorption of laser energy: The laser beam is absorbed by the contaminant or coating on the surface, causing it to heat up rapidly.
- Vaporization or ablation: The heated material either vaporizes or is ablated, leaving behind a clean surface.
- Selective absorption: Different materials absorb laser energy at different rates, allowing for selective removal of contaminants.
- No damage to substrate: Laser cleaning is a precise process that does not damage the underlying substrate.
Laser cleaning can be used on a wide range of materials, including metals, plastics, ceramics, and composites. It is particularly effective for removing rust, paint, grease, and other stubborn contaminants.
Advantages of laser cleaning
There are several advantages to using laser cleaning over traditional cleaning methods:
- Non-contact: Laser cleaning does not require physical contact with the surface, reducing the risk of damage.
- Non-abrasive: Unlike sandblasting or chemical cleaning, laser cleaning does not leave behind any residue or damage the surface.
- Precision: Laser cleaning is a highly precise process that can be controlled to remove only the desired material.
- Environmentally friendly: Laser cleaning does not produce any waste or harmful chemicals, making it an eco-friendly option.
In conclusion, laser cleaning is a versatile and efficient method of removing contaminants from surfaces. Its principles are based on the absorption of laser energy, vaporization or ablation of unwanted material, selective absorption, and no damage to the substrate. With its many advantages, laser cleaning is a popular choice for industries looking for a clean and environmentally friendly solution.
#laser cleaning, principles, contaminants, coatings, oxides, non-contact, non-abrasive, vaporize, ablate, selective absorption, substrate, advantages, precision, environmentally friendly
#highly effective method, wide range of materials, rust removal, paint removal, grease removal, non-contact cleaning, eco-friendly option
The different types of lasers used for cleaning applications
1. Fiber lasers
Fiber lasers are one of the most commonly used types of lasers for cleaning applications. They are known for their high power output, efficiency, and reliability. Fiber lasers are capable of removing a wide range of contaminants, including rust, paint, grease, and oxides, from various surfaces. They are also highly versatile and can be used for cleaning delicate materials without causing damage.
2. CO2 lasers
CO2 lasers are another popular choice for cleaning applications. They are particularly effective for removing organic contaminants, such as dirt, oil, and grease, from surfaces. CO2 lasers operate at a wavelength of around 10.6 microns, which makes them ideal for cleaning applications where precision is required. They are also relatively affordable and easy to maintain.
3. Nd:YAG lasers
Nd:YAG lasers are commonly used for cleaning applications that require high precision and control. They operate at a wavelength of around 1.06 microns, which allows them to remove contaminants with minimal heat input. Nd:YAG lasers are often used for cleaning delicate materials, such as electronics components, without causing damage. They are also highly efficient and can be used for both surface cleaning and ablation.
4. Excimer lasers
Excimer lasers are specialized lasers that are used for cleaning applications that require ultra-precision and minimal thermal damage. They operate at ultraviolet wavelengths, which allows them to remove contaminants with high precision and minimal heat input. Excimer lasers are often used for cleaning semiconductor materials, optics, and other sensitive components.
In conclusion, the use of lasers for cleaning applications offers a wide range of benefits, including increased efficiency, precision, and environmental friendliness. Each type of laser has its own unique characteristics and advantages, making them suitable for different cleaning applications. By choosing the right type of laser for a specific cleaning task, businesses can achieve optimal results while minimizing costs and environmental impact.
- Fiber lasers
- CO2 lasers
- Nd:YAG lasers
- Excimer lasers
#laser #cleaning #technology #fiber #CO2 #NdYAG #Excimer
frazy kluczowe:
types of lasers for cleaning applications, benefits of laser cleaning, laser cleaning technology, laser cleaning methods, laser cleaning equipment
The safety precautions and regulations for using lasers in cleaning processes
Safety Precautions:
- Wear appropriate protective gear, such as safety glasses and gloves, to protect against potential hazards.
- Ensure the work area is well-ventilated to prevent the buildup of fumes or dust particles.
- Keep a safe distance from the laser beam to avoid accidental exposure to radiation.
- Regularly inspect and maintain the laser equipment to ensure it is in good working condition.
Regulations:
- Comply with all local, state, and federal regulations regarding the use of lasers in cleaning processes.
- Obtain any necessary permits or licenses before using lasers for cleaning purposes.
- Follow manufacturer guidelines for the safe operation of laser equipment.
- Train employees on proper laser safety procedures and protocols.
By following these safety precautions and regulations, businesses can ensure that laser cleaning processes are carried out safely and effectively, minimizing the risk of accidents or injuries.
Hashtags:
#lasersafety #cleaningprocess #safetyregulations
Keywords:
Laser cleaning, safety precautions, regulations, protective gear, ventilation, radiation exposure, equipment maintenance, permits, employee training
Long-tail Phrases:
Safety precautions for using lasers in cleaning processes, regulations for laser cleaning, importance of laser safety, effective laser cleaning methods
The potential hazards of laser cleaning and how to mitigate them
Potential hazards of laser cleaning
There are several potential hazards associated with laser cleaning, including:
Hazard | Description |
---|---|
Eye damage | Laser beams can cause permanent eye damage if proper eye protection is not worn. |
Skin burns | High-intensity laser beams can cause burns to the skin if proper protective clothing is not worn. |
Toxic fumes | Some materials, when heated by a laser beam, can release toxic fumes that are harmful to inhale. |
Fire hazard | Laser beams can ignite flammable materials, leading to a fire hazard. |
How to mitigate hazards
To mitigate the hazards associated with laser cleaning, follow these tips:
Tip | Description |
---|---|
Use proper eye protection | Ensure that all workers wear appropriate laser safety goggles to protect their eyes from laser beams. |
Wear protective clothing | Workers should wear flame-resistant clothing and gloves to protect their skin from burns. |
Ventilate the work area | Ensure that the work area is well-ventilated to prevent the buildup of toxic fumes. |
Keep flammable materials away | Avoid using laser cleaning near flammable materials to reduce the risk of fire. |
By following these tips, you can help mitigate the potential hazards associated with laser cleaning and ensure the safety of workers and the environment.
#laser #cleaning #hazards #safety #mitigation
The potential applications of laser cleaning in different industries
In the automotive industry, laser cleaning can be used to remove paint, rust, and other contaminants from car bodies, engine components, and other parts. This not only improves the appearance of the vehicle but also helps to prolong its lifespan by preventing corrosion and other forms of damage. Laser cleaning can also be used in the aerospace industry to remove coatings and contaminants from aircraft components, ensuring optimal performance and safety.
In the manufacturing sector, laser cleaning can be used to prepare surfaces for welding, painting, or other processes by removing oxides, oils, and other contaminants. This helps to improve the quality and durability of the finished products while reducing the need for manual labor and chemical cleaning agents. In the electronics industry, laser cleaning can be used to remove solder flux, adhesives, and other residues from circuit boards and other components, improving the reliability and performance of electronic devices.
Overall, the potential applications of laser cleaning are vast and varied, with the technology offering benefits in terms of efficiency, cost-effectiveness, and environmental sustainability. As the technology continues to advance and become more widely adopted, it is likely to play an increasingly important role in a wide range of industries.
#laser #cleaning #technology #precision #versatility #automotive #aerospace #manufacturing #electronics #efficiency #environmental #sustainability
frazy kluczowe:
– Innovative laser cleaning technology
– Precision cleaning with high-powered lasers
– Versatile applications in various industries
– Environmentally friendly alternative to traditional methods
– Improved quality and durability of finished products
– Cost-effective and efficient cleaning solution
– Potential for widespread adoption in the future
The potential health effects of exposure to laser cleaning emissions
Potential health risks
Exposure to laser cleaning emissions can pose several health risks, including:
Health Risk | Description |
---|---|
Eye damage | Direct exposure to laser beams can cause damage to the eyes, leading to vision problems or even blindness. |
Skin burns | Exposure to high-intensity laser beams can result in skin burns, which can be painful and may require medical treatment. |
Respiratory issues | Inhalation of laser cleaning emissions can irritate the respiratory system and lead to breathing difficulties. |
Cancer risk | Some studies suggest that long-term exposure to certain laser cleaning emissions may increase the risk of developing cancer. |
Ways to mitigate risks
To reduce the potential health risks associated with exposure to laser cleaning emissions, it is important to take the following precautions:
- Use appropriate personal protective equipment, such as safety goggles and gloves, when working with laser cleaning equipment.
- Ensure that the work area is well-ventilated to minimize exposure to laser cleaning emissions.
- Follow proper safety protocols and training when operating laser cleaning equipment.
- Regularly monitor and maintain laser cleaning equipment to ensure it is functioning properly and emitting safe levels of radiation.
By taking these precautions, workers can minimize their risk of exposure to laser cleaning emissions and protect their health.
Conclusion
While laser cleaning technology offers many benefits, it is important to be aware of the potential health risks associated with exposure to laser cleaning emissions. By following proper safety protocols and taking precautions, workers can minimize their risk of harm and continue to safely use this technology in various industries.
#healthrisks #laseremissions #safetyprotocols #personalprotectiveequipment #respiratoryissues #skindamage #cancerrisk #visionproblems #safetytraining
Keywords: laser cleaning emissions, health risks, safety protocols, personal protective equipment, respiratory issues, skin damage, cancer risk, vision problems, safety training
Long-tail phrases: potential health effects of exposure to laser cleaning emissions, ways to mitigate risks associated with laser cleaning emissions, precautions for working with laser cleaning equipment, importance of proper safety protocols in laser cleaning operations.
The role of quality control measures in ensuring the effectiveness and safety of laser cleaning processes
Quality control measures play a crucial role in the success of laser cleaning processes by:
1. Monitoring the laser parameters: The power, wavelength, pulse duration, and spot size of the laser beam must be carefully controlled to ensure that the cleaning process is effective and safe. Any deviations from the optimal parameters can result in incomplete cleaning or damage to the substrate.
2. Checking the cleanliness of the surface: Before and after the cleaning process, the cleanliness of the surface should be assessed using techniques such as microscopy or spectroscopy. This helps to ensure that the contaminants have been completely removed without leaving any residues behind.
3. Evaluating the surface roughness: Laser cleaning can alter the surface roughness of the substrate, which may affect its performance or appearance. Quality control measures should include the measurement of surface roughness to ensure that it meets the required specifications.
4. Monitoring the temperature: Laser cleaning generates heat, which can potentially damage the substrate if not controlled properly. Temperature monitoring during the cleaning process is essential to prevent overheating and ensure the safety of the operators.
5. Conducting safety assessments: Before implementing laser cleaning processes, a thorough safety assessment should be conducted to identify potential hazards and risks. This includes assessing the laser safety measures, personal protective equipment, and emergency procedures.
Overall, quality control measures are essential for:
– Ensuring the effectiveness and safety of laser cleaning processes
– Preventing damage to the substrate
– Minimizing risks to the operators
– Achieving consistent cleaning results
In conclusion, quality control measures are indispensable in ensuring the success of laser cleaning processes. By monitoring the laser parameters, checking the cleanliness of the surface, evaluating the surface roughness, monitoring the temperature, and conducting safety assessments, the effectiveness and safety of laser cleaning can be guaranteed.
#qualitycontrol #laser #cleaning #safety #effectiveness
Keywords: laser cleaning, quality control measures, safety assessment, surface roughness, temperature monitoring
Long-tail phrases: “importance of quality control in laser cleaning”, “ensuring safety in laser cleaning processes”, “monitoring laser parameters for effective cleaning”
The potential impact of laser cleaning on worker productivity and efficiency
In addition to its speed, laser cleaning also offers a higher level of precision than traditional cleaning methods. The focused beam of the laser can target specific areas with pinpoint accuracy, ensuring that only the dirt and grime are removed without damaging the underlying surface. This precision can help workers avoid costly mistakes and reduce the risk of damage to equipment, further increasing efficiency in the workplace.
Furthermore, laser cleaning is a non-contact process, meaning that workers do not need to come into direct contact with the surfaces being cleaned. This can help reduce the risk of injury and exposure to harmful chemicals, creating a safer working environment for employees. By minimizing the risk of accidents and injuries, laser cleaning can help improve worker morale and job satisfaction, leading to increased productivity and efficiency.
Overall, is significant. By offering a faster, more precise, and safer alternative to traditional cleaning methods, laser cleaning can help workers complete tasks more quickly and effectively, leading to increased productivity and efficiency in the workplace.
#laser cleaning #worker productivity #efficiency #industrial equipment #precision cleaning #non-contact cleaning
frazy kluczowe:
– cutting-edge technology for industrial cleaning
– fast and efficient cleaning method
– precise and safe cleaning process
– increased worker productivity and efficiency
– environmentally friendly cleaning solution
- Laser cleaning for removing adhesive residues - 25 July 2024
- The safety considerations of laser cleaning - 16 April 2024
- Applications of laser cleaning in the automotive industry - 21 January 2024